In machining or metal cutting, relative velocity between cutting tool and workpiece is mandatory in order to cut (shear off) excess material from workpiece to get desired shape, size, finish and tolerance. Every machining process requires three relative motions namely cutting velocity, feed rate and depth of cut. Such motions are imparted in several ways in various directions depending on the process and requirement. For example, in straight turning operation in Lathe, cutting velocity, feed rate and depth of cut are given in three mutually perpendicular directions.
Evolution of cutting speed and cutting velocity terms
During machining, cutting velocity (one of the important process parameters) can be applied in four distinct ways, as listed below.
- Rotating workpiece (For example, lathe operations).
- Rotating tool (For example, milling, drilling, and grinding operations).
- Reciprocating workpiece (For example, planing operation).
- Reciprocating tool (For example, shaping and slotting operations).
When either tool or workpiece is rotating, its rotational characteristics can be expressed in two ways. First one is by specifying the number of revolutions per unit time (measured in rpm), and second one is by specifying tangential velocity at a point in the body (measured in m/min). First one is basically cutting speed (a scalar quantity); whereas the second one is cutting velocity (a vector quantity). Irrespective of type of motion (rotational or reciprocating), cutting velocity will always exist there. In reciprocating type motion, the linear velocity of the tool or workpiece is the desired cutting velocity. However, cutting speed term will be irrelevant when motion type is reciprocating because of the absence of any rotating part.
What is cutting speed?
Cutting speed is the rotational speed of either workpiece or cutting tool (based on which is rotating). It is measured by the unit—revolution per minute (rpm) and designated by N. For example, cutting speed in turning is 295rpm.
In case lathe operations, such as turning, grooving, centre drilling, parting, etc., a cylindrical workpiece is used. Here the workpiece is rotated at certain speed while the cutting tool is kept fixed. Therefore, the rotational speed of cylindrical workpiece is known as Cutting Speed, which is measured in rpm.
On the other hand, for milling, drilling and grinding operations, the cutting tool (known as milling cutter, drill and grinding wheel, respectively) is of cylindrical shape and thus it rotates at certain speed while the workpiece is kept fixed. So in this case, the rotational speed of the cutting tool is nothing but Cutting Speed, which is also measured in rpm.
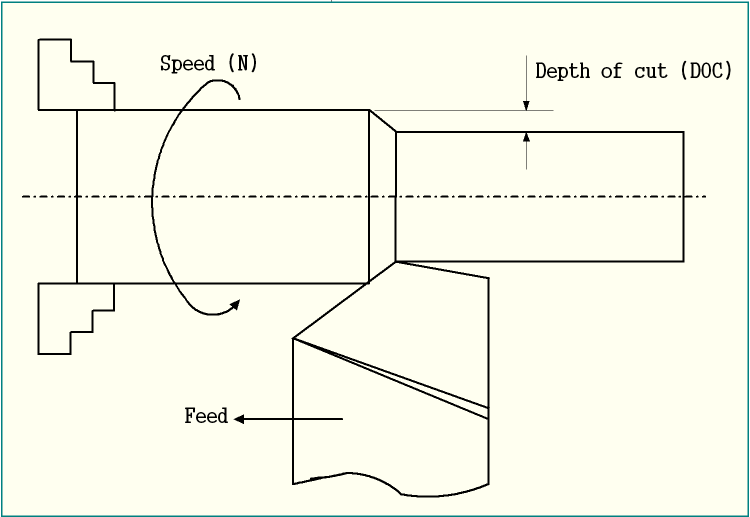
What is cutting velocity?
It is the tangential velocity of either the rotating workpiece or the rotating cutting tool. It is measured by the unit—meters per minute (m/min) and designated by Vc. Any rotating object has a tangential velocity at any point on its body except the axis of rotation (velocity is zero at axis). For the same rotational speed, with increase in radial distance from axis of rotation, cutting velocity proportionally increases. Therefore maximum velocity can be obtained at the periphery of either the cutter or workpiece.
Unlike cutting speed, which is a scalar quantity, cutting velocity is a vector and its direction changes from one point to another on the periphery of the workpiece or cutting tool. There are few other differences among them. For detail, you may follow the below links. However, cutting speed can be converted into cutting velocity or vice versa, as discussed below.
Typical values for cutting velocity and speed
Selection of value for cutting velocity for a particular machining operation needs consideration on a large number of factors including intended productivity, surface quality, tool life and also machine capability. Usually, a combination of machining process, tool material and work material gives a typical range for cutting velocity and thereafter a suitable value is chosen from that range based on other parameters.
If required, cutting speed can be calculated from the selected velocity, with the help of conversion formula (provided below) and using the diameter of tool or workpiece (whichever is rotating). Typical values for cutting velocity for several tool materials are provided below.
- High Speed Steel (HSS): 20 – 40m/min.
- Plain carbide: 80 – 100m/min.
- Coated carbide tool: 120 – 150m/min.
- Ceramic tool: 150 – 400m/min.
- Cubic boron nitrite (cBN) cutter: 300 – 600m/min.
- Diamond tool: 300 – 500m/min.
Conversion from cutting speed to cutting velocity
If the diameter/radius of the workpiece or cutting tool is known then you can absolutely convert one to another. Their relation can be expressed by a simple equation as provided below. Take care of the unit of each parameter while such conversion.
$${V_c} = {{\pi .D.N} \over {1000}}$$
- Vc = Cutting velocity (m/min)
- D = Diameter of workpiece or cutting tool (mm)
- N = Cutting speed (rpm)
Problem: While turning a 10cm diameter workpiece at a speed of 300rpm, what would be the cutting velocity?
$${V_c} = {{\pi \times 100 \times 300} \over {1000}} = 94.3m/min $$
Why it is necessary to determine cutting velocity?
The simple answer is—to choose cutting tool material and other machining parameters. Every cutting tool material has a maximum and minimum limit of cutting velocity within which it can perform satisfactorily. For example, an HSS (High Speed Steel) can be used between 15 – 40m/min; whereas a diamond tool can be used between 300 – 500m/min.
Since diameter of workpiece or cutting tool can vary extensively, so for the same cutting speed, cutting velocity will change greatly. Therefore cutting speed cannot be used for choosing tool material. Except this, there are many other analytical expressions which use cutting velocity term. Such expressions are developed to assess cutting force, temperature, vibration, machinability, economy of machining, etc. So it is indispensably necessary to determine cutting velocity from cutting speed using above expressions.
Influence of cutting velocity on machining performance
Since cutting velocity is one important cutting parameter, its value influences overall machining performance including built-up edge (BUE), type of chip, restricted cutting effect (RCE), cutting force, power consumption, vibration, deflection, cutting temperature, MRR, surface finish or roughness, tool life, cutting time and machining economics.
In general, higher velocity enhances material removal rate (MRR), which consequently improves productivity and reduces machining time substantially. Significantly high velocity also degrades the changes of BUE enlargement. However, cutting force, vibration and cutting temperature increase proportionally with velocity. For detail, you may read effects of cutting velocity on machining performance. Therefore, an optimization is beneficial for selecting appropriate cutting velocity for a particular process under specific conditions.
References
- Book: Machining and Machine Tools by A. B. Chattopadhyay (Wiley).
- Book: Metal Cutting: Theory And Practice by A. Bhattacharya (New Central Book Agency).