Main reason for roughness of the machined surface is presence of feed marks or scallop marks, which is inherent to conventional machining because of the depth of cut and feed velocity. Apart from roughness, surface integrity term also consists of several topological and metallurgical characteristics. In practice, there are several factors that directly and indirectly influence overall quality of a machined surface. Such common factors are illustrated with the help of cause and effect diagram, as depicted below. Various steps that can be considered to improve surface integrity in machining are also enlisted below.
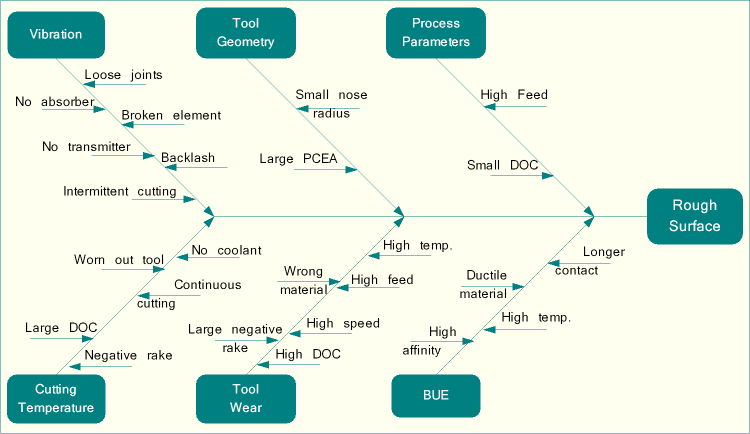
Tight control of process parameters
Reduce feed rate as far as possible. Roughness parameter is proportional to the feed rate, so lower feed rate can help improving surface finish. High feed rate increases material removal rate (MRR) but accelerates tool wear and cutting temperature, which have undesirable impact on overall surface quality.
Increase depth of cut. This can improve stock removal rate (i.e., MRR) without increasing roughness parameter. However, cutting force, cutting temperature and tool wear rate usually increase with DOC, which can hamper overall quality of machined surface if exceeds beyond a limit.
Choosing appropriate cutting tool
Use rounded tip tool. For same feed rate and depth of cut, a rounded tip tool can provide considerably smoother surface compared to a sharp tool. So cutting tools having a small nose radius can improve surface finish; however, high nose radius may degrade surface integrity by increasing rate of heat generation and shear deformation (large negative rake angle).
Reduce principal and auxiliary cutting edge angles. Choose such single point cutting tool that has smaller principal cutting edge angle (φ) and auxiliary cutting edge angle (φ1).
Modify tool tip. A modified tool with flattened tip can substantially improve surface finish. However, such tools are costlier.
Select compatible tool material. Tool material should have to be compatible with work material, otherwise tool wear rate will increase and tool life will decrease. Worn out or damaged tool can severely hamper surface integrity by making rake angle highly positive (this is totally undesirable as it causes large shear deformation, high power consumption, high cutting temperature, etc.).
Control vibration in machine tool
Maintain machine tool regularly. Any loose elements, broken parts, backlash and also worn out or broken cutters can induce vibration in machine tool. So by properly maintaining the machines and lubricating various elements, chances of vibration can be reduced. This indirectly helps improving surface integrity.
Transmit or absorb vibration. Machine tools must be capable of transmitting vibration to the ground. Usage of vibration absorber can also keep vibrations at the bay.
Avoid intermittent cutting. Such cutting processes inherently induce vibration.
Control cutting temperature
Use cutting fluid. Usage of cutting fluid can protect workpiece and tool from detrimental effects of high cutting temperature by reducing rate of heat generation and removing generated heat.
Use tool with positive rake. A negative rake tool increases shear deformation and cutting temperature. So use of positive rake can help improving surface finish.
Replace tools timely. A worn out tool can accelerate cutting heat generation and thus timely replacement of cutting tools is indispensably necessary.
Eliminate chances of BUE formation
Use sensors. Built up edge (BUE) increases cutting force and vibration. Thus sensors can be used to record such statements and thus necessary actions can be taken for reducing chances of BUE formation.
Longer chip-tool contact. Longer contact can increase chances of BUE formation, and thus reducing contact length (such as by using chip breaker), surface finish can be indirectly improved.
References
- Paper: F. Jafarian, H. Amirabadi and M. Fattahi (2014); Improving surface integrity in finish machining of Inconel 718 alloy using intelligent systems; The International Journal of Advanced Manufacturing Technology; Vol. 71; pp. 817–827.
- Book: Surface Integrity in Machining by J. P. Davim (Springer).
- Book: Machining and Machine Tools by A. B. Chattopadhyay (Wiley).
- Book: Metal Cutting: Theory And Practice by A. Bhattacharya (New Central Book Agency).